* Since the electrodes with smaller diameters than those of coated electrode arc welding, it has a higher current density and highermetal accumulation speed in same current range.
2. The welding metal obtained with inert gas welding has a low hydrogen content, which is highly beneficial in steels with hardening properties.
3. Since deep ingression is possible in inert gas welding, it is possible to make small corner welds and it provides a smoother root penetration compared to coated electrode arc welding.
4. Although the thin materials are usually welded with TIG welding method with or without using additional metal, the inert gas welding gives better results on the welding of thin materials than coated electrode arc welding.
5. It is highly suitable for use in both semi-automatic and full-automatic welding systems.
Disadvantages:
1. The inert gas welding equipment are more complex, more expensive and more difficult to transport than coated electrode arc welding equipment.
2. Since the inert gas welding torch should be close to the workpiece, it is more difficult to weld in hardly accessible areas compared to coated electrode arc welding.
3. The welding joints made with inert gas welding on steels having hardening property is more prone to cracking since there is no slag layer that decreases the cooling speed of the welding metal as is the case in coated electrode arc welding.
4. The inert gas welding requires additional protection against airflow to send away the gas protection from the welding area. Therefore, it is not as suitable as coated electrode arc welding for welding works in outdoor areas.
CORED WIRE ARC WELDING
Arc welding with cored wire is an arc welding method where the heat necessary for the welding is generated by the arc formed between a wasting cored wire electrode and the workpiece. The protection of arc and welding area is provided by the gases formed as a result of burning and separation of the elementary substance in the cored wire or by an externally supplied protective gas as is the case in inert gas welding. The self-protected (open, arc based welding wires) welding process is rather similar to the gas protection in coated electrode welding method. The coating material on coated electrodes causes production of flat bar shaped electrodes and the length restrictions. In cored wires, however, this coating material is formed in the shape of a wire wrapped on a roller, since the tubular wire is within the electrode, and may be supplied to the continuous welding area.
This welding method may be applied for both semi-automatic and full-automatic welding systems.
The disadvantage of welding with cored wire is that a slag layer, which is similar to that in coated electrode arc welding but is a little thinner, is formed on the weld bead. However, many types of cored wire electrodes that don't require slag removal or don't generate slag are being manufactured today.
TIG WELDING
TIG welding is an arc welding method where the heat necessary for the welding is generated by the arc formed between a non-wasting electrode (tungsten electrode) and the workpiece. The electrode, welding bath, arc and the areas of the workpiece near to the welding machine are protected against the hazardous impact of the atmosphere by the gas or mixed gas supplied from the welding torch. The gas should be able to fully protect the welding area, otherwise a very small air ingression causes errors on the welding metal.
Benefits:
1. The TIG welding is suitable for both manual and automatic welding systems to make continuous weld beads, intermittent welds and spot welds. 2. Since the electrode is not wasted (consumed off) welding is performed by melting the base metal or using an additional welding metal. 3. Welding may be performed in any position and it is particularly suitable for welding of thin materials. |  |
4. It provides high-ingression and non-porous welds in root pass welding works.
5. Since the heat input is concentrated on the welding area, the workpiece is slightly deformed.
6. It also provides a smooth weld bead and removing the weld bead is not necessary.
Disadvantages:
1. The metal accumulation speed of TIG welding is lower compared to other arc welding methods.
2. It is not an economical method in welding of thick-sectioned materials.
Submerged welding is an arc welding method where the heat necessary for the welding is generated by the arc(s) formed between a wasting electrode (or several electrodes) and the workpiece. The arc area welding powder layer as well as the welding metal and base metal close to the weld are protected by the melted welding powder (slag). In submerged welding the electricity flows through the arc and the welding bath consisting of melted metal and melted slag. The arc heat electrode forms the welding bath that fills up the welding bend by melting the melting powder and base metal. The welding powder acting as a protective element also reacts with the welding bath and deoxidizes the welding metal. The welding powders used for welding the alloy steels may contain alloy elements that compensate the chemical composition of welding metal. Submerged welding is an automatic welding method. In some submerged arc welding applications two or more electrodes may be concurrently fed into the welding bend. The electrodes may be fed into the welding bath as a twin arc or may be successively fed with a distance sufficient to ensure that the welding baths are individually hardened and thereby a high welding speed and high metal accumulation speed may be obtained.
| 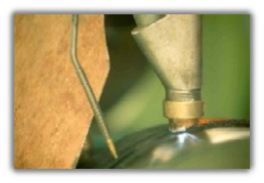 |
Benefits:
1. It is a welding method with high welding speed and high metal accumulation speed that may be used for welding of flat and cylindrical parts, tubes with any thickness and size as well as for brazing filler welds.
2. It provides perfect and mechanically resilient weld beads.
3. Since there is no spattering and the arc lights are invisible, the level of protection required to protect the welding operator is less.
4. It is possible to weld the welding bend angles contrary to other methods.
5. The submerged welding may be performed in both indoor and outdoor areas.
Disadvantages:
1. The submerged welding powders are prone to take in moisture from the air, which causes pores in welding.
2. The base metal should be flat and smooth and no oil, rust or other impurities should exist on the base metal in order to obtain high-quality welds.
3. The slag should be removed off the weld bead and this may be difficult in some applications. In multi-pass welding works, the slag should be removed after each pass to prevent slag residuals.
4. The submerged welding method is not suitable for materials thinner than 5 mm since it may cause oxidation.
5. This method is suitable for butt-welding and corner welds on flat and horizontal spaces with the exception of some applications.